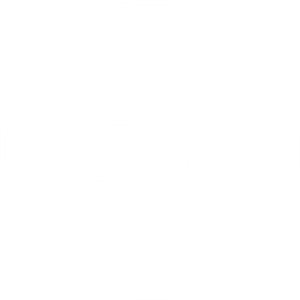
Whatever your requirements are for an industrial watertube boiler, John Thompson can tailor-design a solution for you.
Irrespective of the industry you serve – from food and beverage, to sugar, pulp and paper, chemical, petrochemical, iron and steel, mining, marine or textiles, we can design, build, install and maintain a cost-effective watertube boiler for the task. With a reputation for reliability and proven performance built right in, John Thompson’s watertube boilers are available in a wide range of capacities and configurations, to suit a variety of fuels and applications. Our service offering includes site installation and commissioning, repair and maintenance, equipment retrofits, capacity and efficiency improvements, operational audits, reliability studies, metallurgical survey and remnant life analysis, operator training and the supply of OEM spares.
Boilers
Whether you require a boiler that’s mono- or bi-drum, single- or multi-pass, top-, bottom- or girth supported, we can offer you designs up to 350 t/h capacity and 110 bar(g), 540 °C steam conditions.
The range includes:
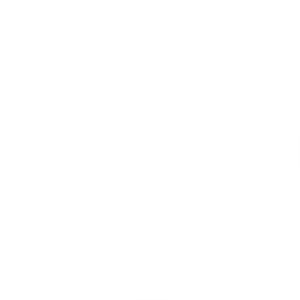
Oil-fired boilers
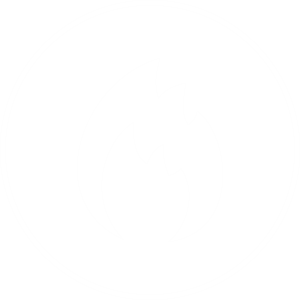
Gas fired boilers
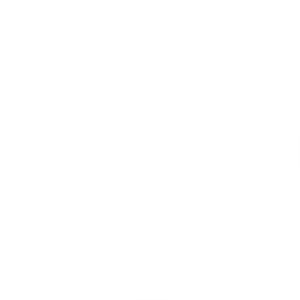
Coal-fired boilers with travelling grates and CAD spreader stokers
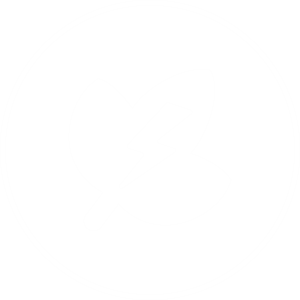
Biomass-fired boilers with CAD spreader stokers, pinhole grates, dump grates and vibrating grates, and
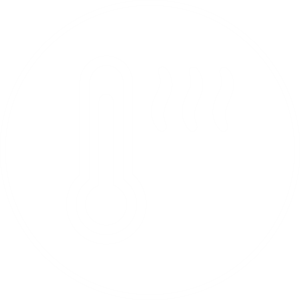
Waste heat recovery boilers
Case Studies
Read how our industrial watertube boilers have solved production challenges for our customers. Click image to view pdf.
Combustion Equipment
Continuous Ash Discharge Stoker
John Thompson steam cleaned pinhole grates are ideal for burning relatively low-ash content biomass fuels. The grates are available in both air- and water-cooled versions.
On a new boiler installation, the floor tubes are typically water-cooled, forming an integral part of the boiler circulation system. The air-cooled version is ideally suited for retrofitting into hearth or "self-feeding" furnaces.
When a pinhole grate is retrofitted to an older boiler, the economics of the situation normally determine the installation of an air-cooled grate in which high pressure rearwall secondary air is passed through the support tubes. This economical arrangement allows for a boiler upgrade without the additional cost of rearranging the boiler pressure parts.
The grate bars are manufactured from temperature resistant cast iron and are profiled to nest closely on the support floor tubes.
Steam jet pressures are controlled to ensure that adequate cleaning is obtained, while at the same time ensuring that erosion is minimised on components that are impinged upon by the steam jets. A multiplicity of jets is employed to ensure that only a small section of the grate is cleaned at any time, thereby ensuring that rapid re-ignition of the fuel is achieved.